was cured using uv lamp intensity of | WT Guide
UV Lamp Intensity: Achieving Effective Curing
Determining the optimal UV lamp intensity for curing applications is crucial for achieving desired material properties and process efficiency. Many professionals struggle to find the balance between curing speed and potential damage to the cured material. This article clarifies the relationship between UV lamp intensity and successful curing.
Understanding UV Curing and Lamp Intensity
UV curing relies on photoinitiators within a material absorbing ultraviolet (UV) light to initiate a polymerization reaction. The intensity of the UV lamp, measured in mW/cm², directly influences the speed and completeness of this process. Higher intensity generally leads to faster curing times, but excessively high intensity can lead to material degradation or uneven curing. Finding the right balance is key.
Factors Affecting Optimal UV Lamp Intensity
Several factors must be considered when determining the appropriate UV lamp intensity:
Material Composition: Different materials have varying sensitivities to UV light. Some require higher intensities for complete curing, while others might degrade with excessive exposure. Manufacturer specifications for your specific material are essential.
Film Thickness: Thicker films require higher intensities or longer exposure times to ensure complete curing throughout.
Lamp Distance: The distance between the lamp and the material influences the intensity received. Closer distances result in higher intensity but increase the risk of uneven curing or overheating.
Conveyor Speed (for continuous processes): In production lines, conveyor speed needs careful adjustment to match the UV lamp intensity and ensure adequate curing time.
Lamp Age and Degradation: UV lamps lose intensity over time. Regular monitoring and replacement are crucial for maintaining consistent curing. This is especially relevant if curing is inconsistent and requires higher energy.
Determining the Optimal Intensity: Practical Tips
Experimentation and careful monitoring are key to finding the perfect UV lamp intensity. Begin by consulting the manufacturer's recommendations for your specific material. Then, conduct controlled experiments, gradually adjusting the intensity and monitoring the resulting cure depth, hardness, and other relevant properties. Consider using a UV radiometer to precisely measure the intensity at the material surface. Analyzing the cured material for defects such as incomplete curing, discoloration, or surface irregularities will help refine your process. Documenting your findings will contribute to optimizing future processes.
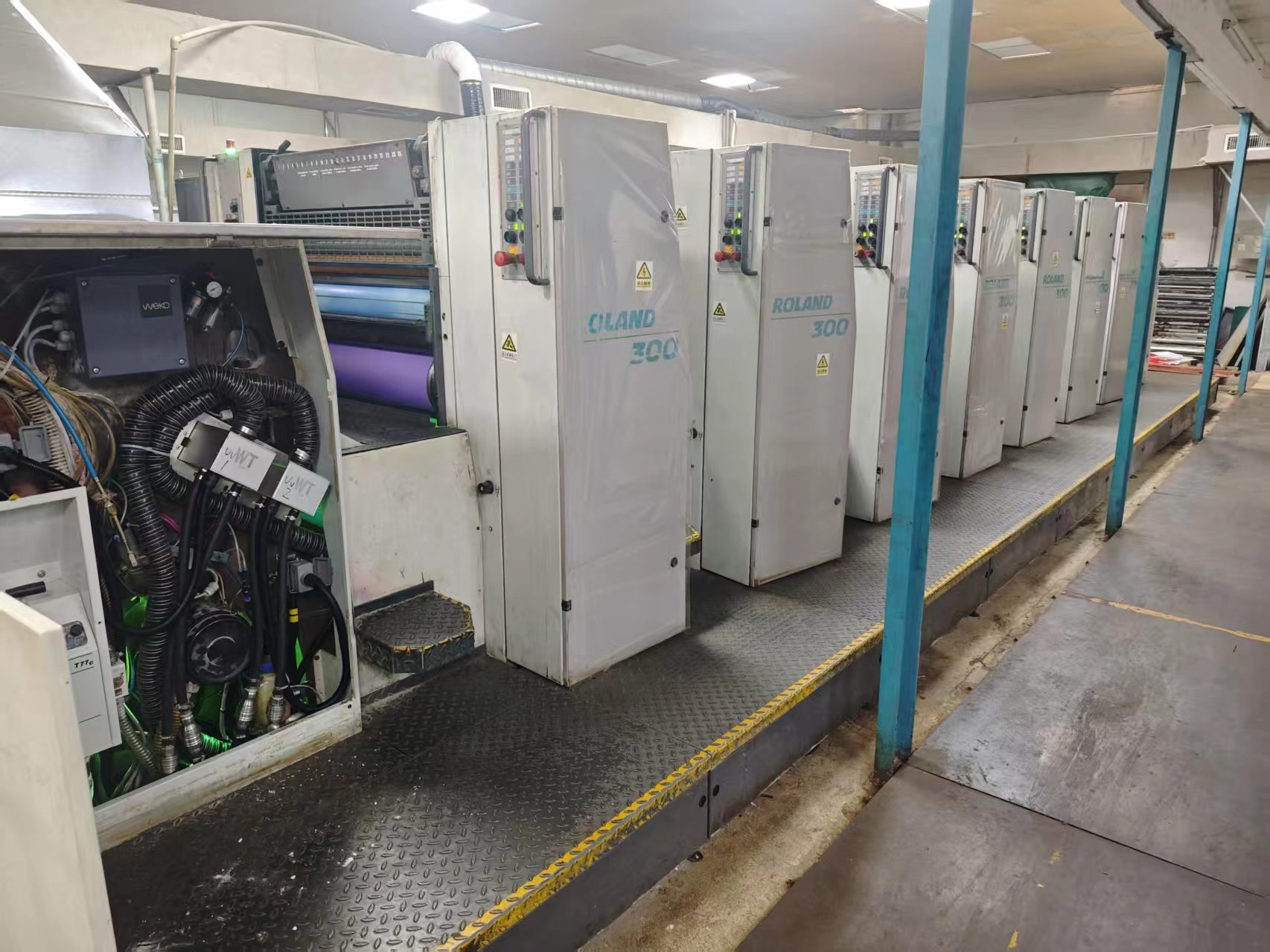
Vtech water-cooled UV/LED system helps Roland 300 printing machine upgrade efficiency again!
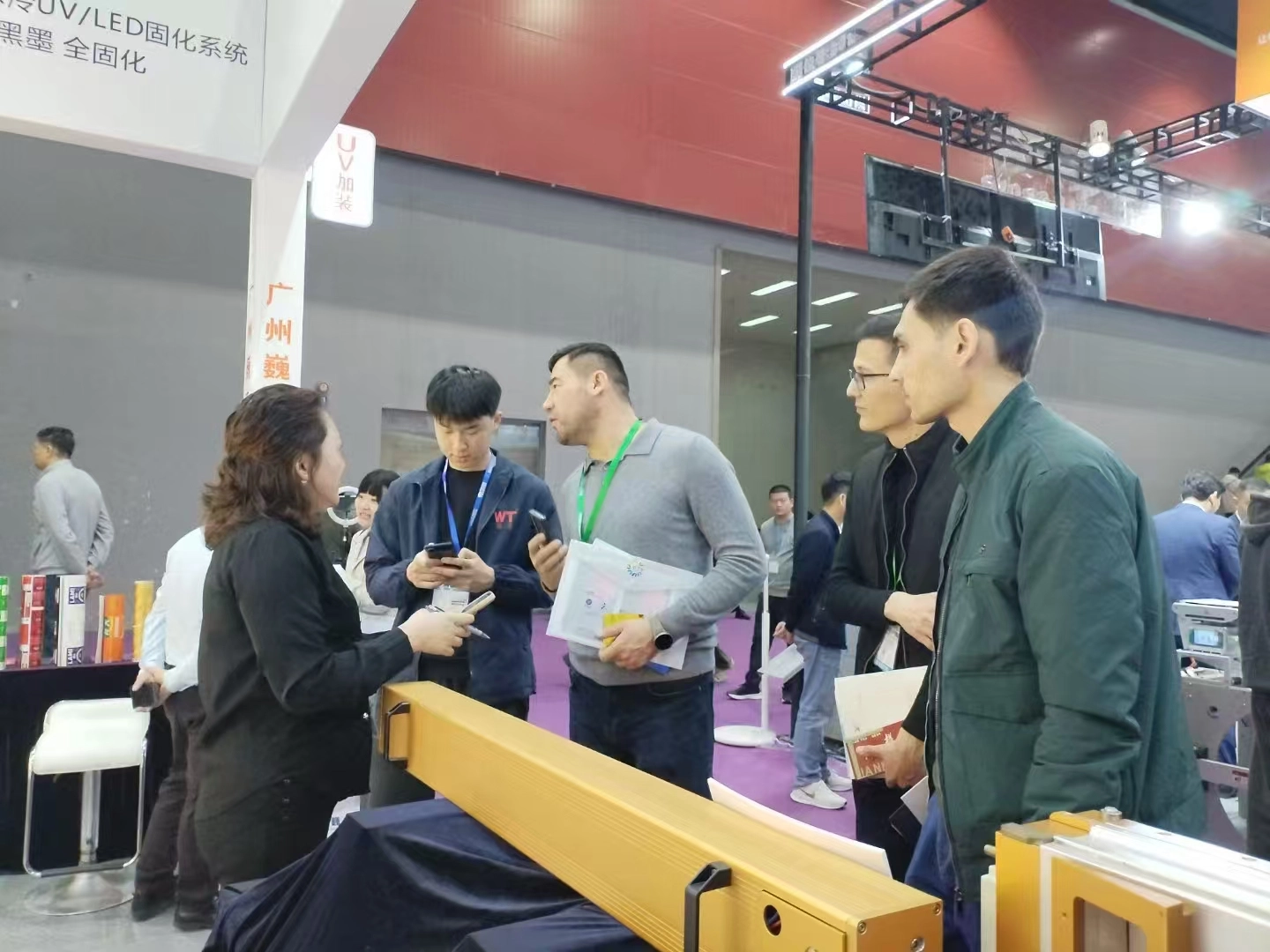
Precision Cooling Solutions Power Global Printing Innovation: Vtech Shines at 2025 South China Printing Expo
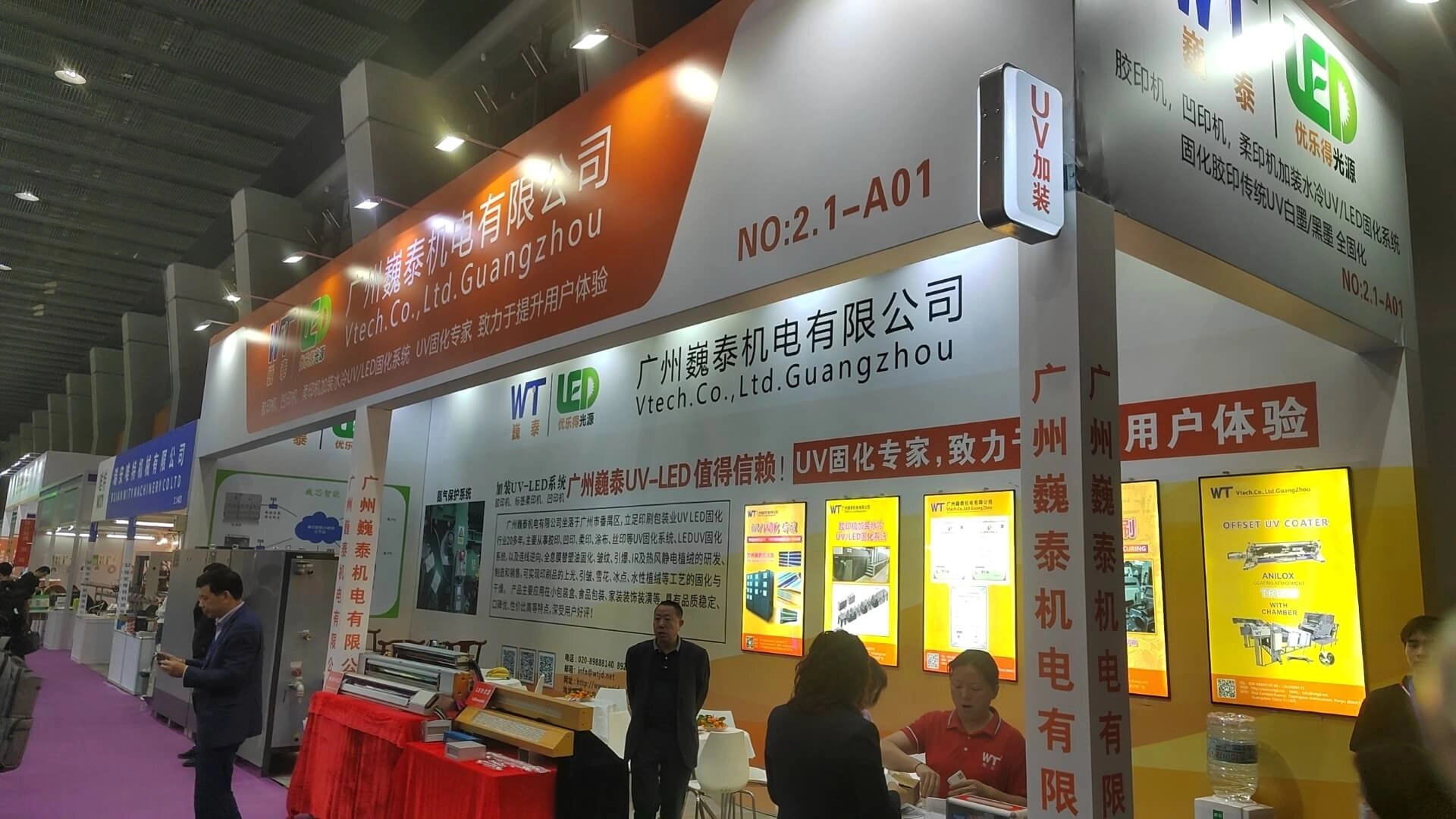
Vtech showcases its innovative water-cooled UV/LED solution at the 2025 South China Printing Exhibition, helping to upgrade printing efficiency
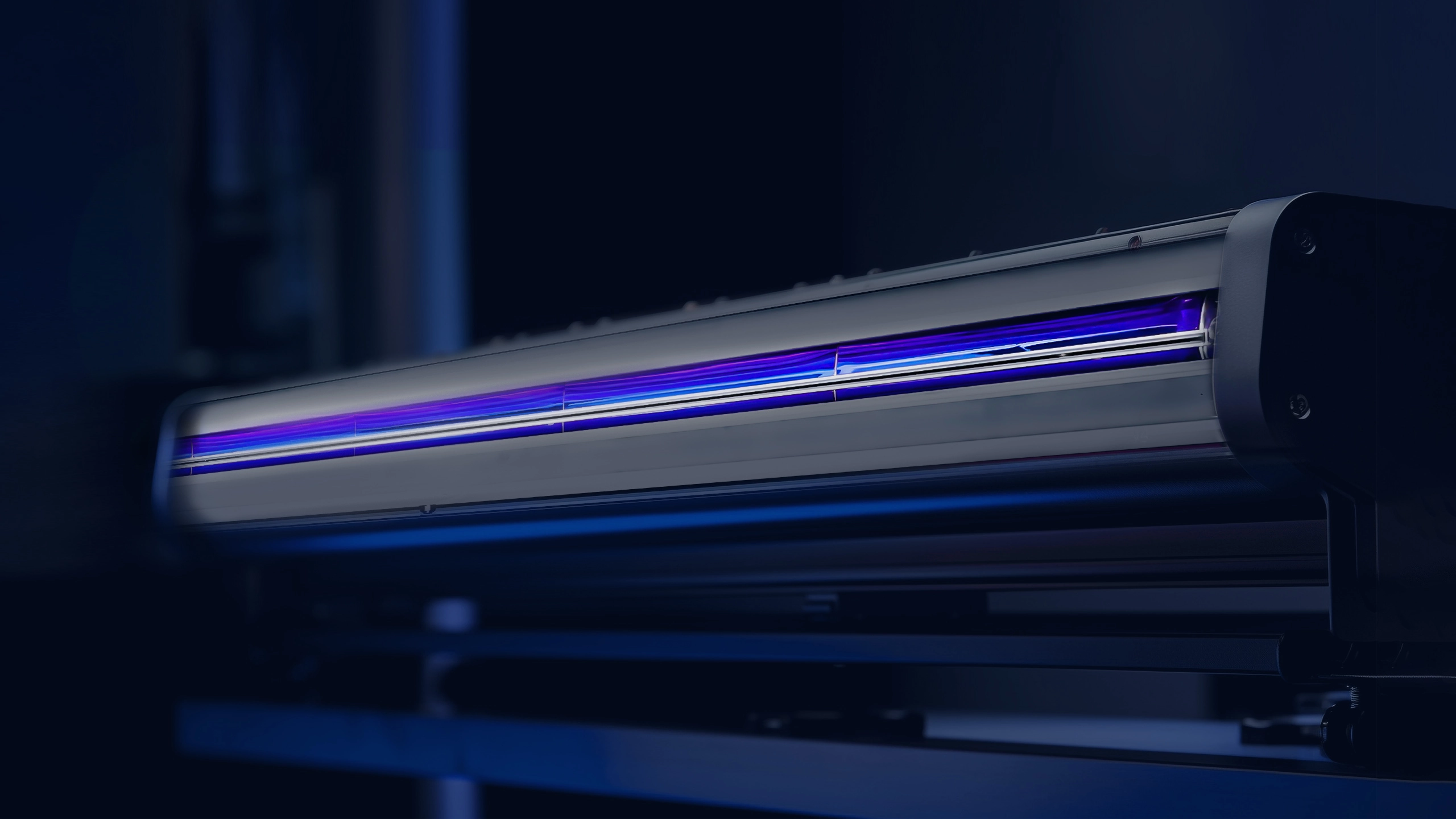
How to choose the best UV light for resin
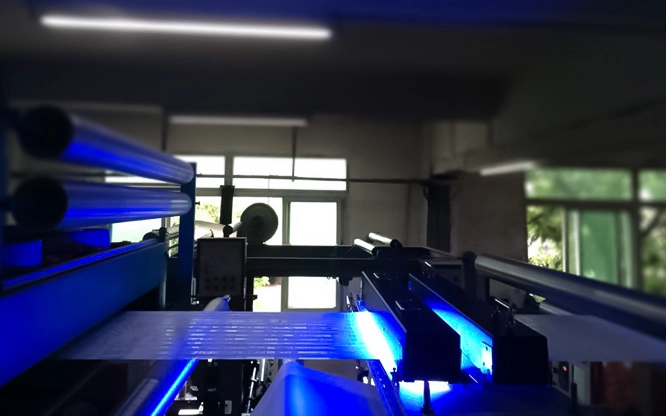
Guidelines for UV Curing: Definition, Principles and Applications
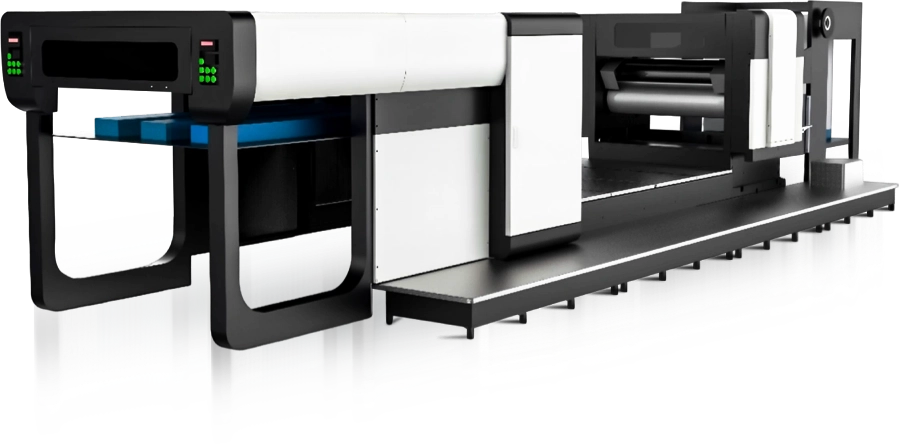
What is the UV printing process? A complete guide to UV printing technology
You may also like
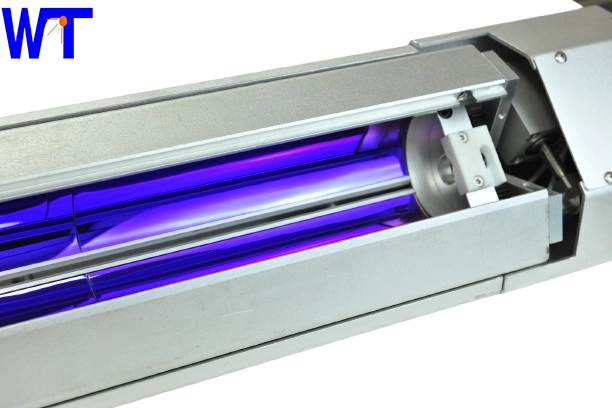
Water cooled UV shutter lampshade
The Water-Cooled UV Shutter lampshade is a high-performance solution designed for modern high-speed printing presses, addressing critical challenges in UV ink and coating curing. By integrating advanced water-cooling technology and a precision shutter mechanism, it ensures stable UV exposure control, minimizes heat generation, and maximizes production uptime for industries requiring rapid, reliable curing processes.
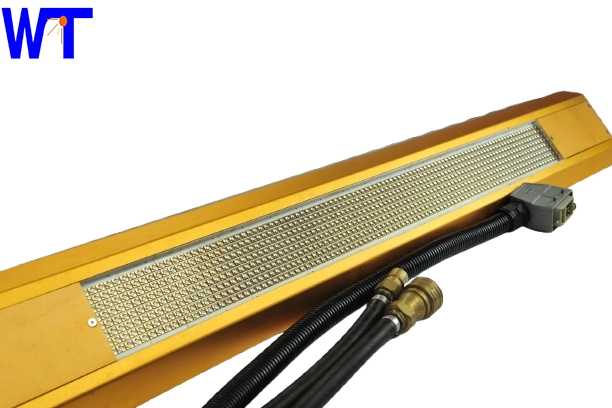
LED water-cooled lampshade
LED water-cooled lampshade is an innovative curing equipment developed specifically for high-speed printing machines. It combines efficient water-cooled heat dissipation technology with high-energy LED light sources, aiming to solve the problems of light source overheating, rapid light decay, and short lifespan caused by long-term high-speed operation of traditional printing equipment. Its core design uses a circulating water cooling system for precise temperature control, ensuring stable output of the light source while meeting the stringent requirements of printing technology for light uniformity, color temperature consistency, and energy conservation and environmental protection. It is an ideal choice for improving printing quality and production efficiency.

UV Dichroic
Dichroic imported from Germany, high-precision color separation, precise control of CMYK dot expansion, adapted to the fast curing characteristics of UV ink, reduces color difference, and is durable
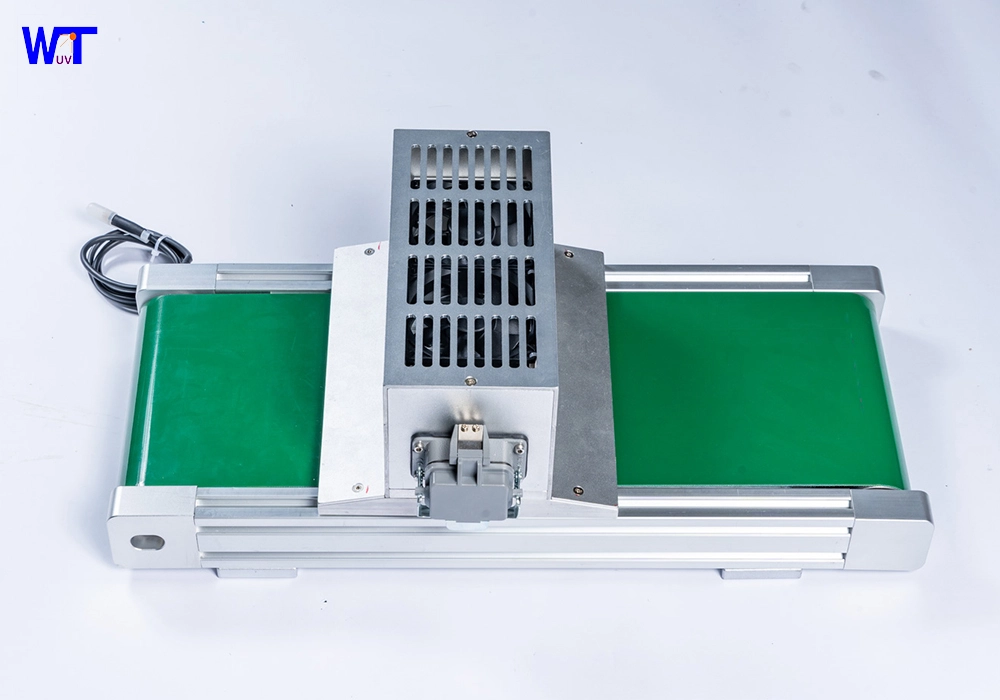
Offset LED pre-press testing machine
Get in touch with us
Copyright © 2023 WTJD.NET All Rights Reserved. | Privacy Policy • Terms and Conditions | Sitemap
vape.king05
WT UV Led Ouyang